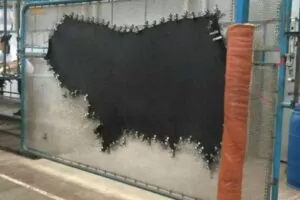
The process of how leather is made hasn’t changed much over the past several thousand years. Finishing techniques and technology have evolved over the years, but the basic process has more or less remained the same.
The entire process of making leather and preparing it for manufacturing is lengthy and complicated, and is performed by skilled artisans, known as tanners. It takes an average of 10 working days to turn hides into finished leather.
The hide of almost any animal can be used to make leather, including sheep, goats, cows, pigs, crocodiles, and even snakes. Cow hides tend to be the most commonly used, due to their larger size and abundance (by-products of the meat and dairy industries) that would otherwise be destroyed.
During this 23-step tutorial, we will show you how leather is made from a salted hide to a high quality piece of leather:
Hides, the term used for animal skins used in leather production, must be preserved, or cured, in order to prevent deterioration. Preservation methods often involve salting, chilling, freezing, or the use of chemicals.
After the hide is cured, it is left soaking in water for several hours, or even days, i order to rehydrate the hide and remove any excess salt, chemicals, or dirt from curing and transportation.
Don’t be confused by the term – in leather making, painting refers to removing the wool from sheep skins, using sulphides.
The primary function of this step is removing any unwanted hair from the hide by introducing alkali. After the hair has been removed, we now have raw animal skin, also referred to as a pelt.
As the name suggests, fleshing is the process of passing the pelt through a machine which removes the tissue from the flesh (back) side. In some cases, a pelt will also be split into layers at this stage.
During this step, the alkali in the pelt is gradually neutralized. This must be done gradually, since rapid change in acidity can cause distortion of the tissue.
Enzymes are now applied to the pelt, which helps to relax and flatten the pelt.
During this step, the salt solutions or weak acids are applied to the pelt. A mildly acidic PH is required for tanning. A strong solution may be applied to preserve the pelts if the tanning won’t occur for several months.
Prior to tanning, excess grease is removed from the pelt with a mild solvent, or water.
Tanning chemically changes the structure of collagen in a pelt, so that it is protected against moisture, chemicals, and microorganisms. In simple terms, proteins in a pelt are converted into a stable material. This can be done several ways including:
Minerals: A mineral, such as salts of chromium (chrome tanned), is the most common leather tanning material. The chrome turns the hides into a bluish color, in which the unfinished hides re referred to as wet-blue.
When splitting the leather, the leather is split horizontally into layers (depending on the thickness, it can be split up to 9 times!), leaving us with a top layer (or top grain leather), and back layers (split leather).
Using the top grain piece, another machine is used to shave the back (non-grain) side, to the desired thickness. Scraps from shaving can be used to make bonded leather and recycled leather.
The leather is hung to dry, generally until the water content is about 20% or less.
Our Designers and Technicians have extensive training in leather making and its use in design and manufacturing.If you would like more information on sourcing or developing custom leather for your collection, contact us for a free consultation.
Not into using leather for your product but need a leather-look?
Read more about Vegan leathers and sustainable options here.
Thread and Butter Design Agency is a full service fashion design agency with global manufacturing partners for handbags, footwear, and apparel.
Thread & Butter takes inspiration from trends around the world and delivers thoughtful, creative design solutions with a whimsical and eclectic attitude. Our work is exciting, demanding, outstandingly creative, and strikes a delicate balance of being of the moment, yet timeless. We are the thread that connects your brand to the world, seamlessly.
Ever wonder how leather is made? Here's the 23-step process of making leather and preparing it for manufacturing handbags, footwear,…
Read moreTega Akinola, a young 22 year old designer from the UK, is turning thrifted socks and sweaters into chic upcycled…
Read moreWhen designing a handbag collection, you may want to create your own custom branded hardware to make your product unique…
Read moreConsumer behaviors, attitudes, and buying habits have all been changed by COVID-19. The overwhelming shift towards eCommerce over in-store experiences,…
Read moreThe massive deal between NIKE and RTFKT paves the way for fashion and a magnificent breakthrough into the world of…
Read moreYou are passionate about fashion. You want to launch a fashion brand or clothing line, but you don't know how…
Read more